Pharmaceutical packaging materials can directly contact drugs, and their quality will affect the safety and stability of drugs. Glass Medicine Bottles have good chemical stability and transparency and can store pharmaceutical products stably. It is one of the most commonly used pharmaceutical packaging materials and has functions unparalleled by other materials. Glass Medicine Bottles containers are divided into several categories according to different standards such as material, performance, molding process, surface treatment after molding, and shape.
Material
According to the different compositions and properties of glass, it is divided into four categories: quartz glass, borosilicate glass, aluminosilicate glass, and soda-lime glass. The main indicators are the content of silicon trioxide and the average linear thermal expansion coefficient. The chemical composition of each type of glass is not constant and fluctuates within a certain range. The chemical composition of the same material of glass is allowed to differ. For example, borosilicate glass is divided into three types, high borosilicate glass, medium borosilicate glass, and low borosilicate glass.
Performance
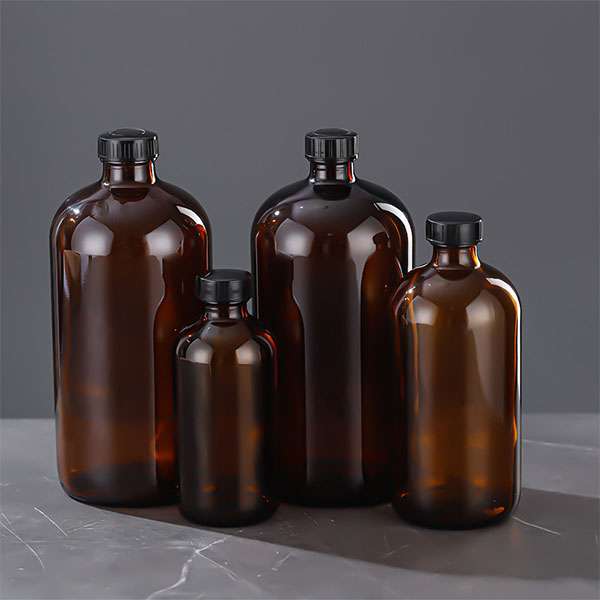
The Glass Medicine Bottles are divided into the following categories according to the water resistance of the particles. When choosing Glass Medicine Bottles, you can find the appropriate medicinal glass based on the characteristics of the drug (such as acid resistance, alkali resistance, high-temperature resistance, etc.). To meet the requirements of drug safety, effectiveness, and quality control.
Type I glass has high water resistance and is suitable for most products for gastrointestinal and non-gastrointestinal uses. Type II glass has been specially treated to achieve high water resistance. It is ideal for most acidic or aqueous products, like alkaline parenteral administration for gastrointestinal and parenteral applications. Type III glass is untreated and is not good for parenteral administration or powders for parenteral administration.
According to the light-shielding properties, it can be divided into two types: colored and colorless. Colorless glass is transparent, easy to observe, and suitable for pharmaceutical packaging. It is not sensitive to light. Different metal oxides are added to the glass for coloring, and the colored glass produces a light-shielding effect. It is suitable for pharmaceutical packaging that requires light protection.
Molding
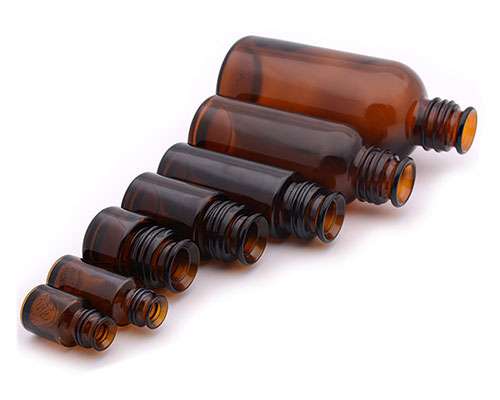
Pharmaceutical glass containers can be divided into molded and tube bottles according to different molding processes. Molded Glass Medicine Bottles are a one-time molding process with thick walls, high mechanical strength, and good surface performance uniformity. The product has a wide range of specifications and can be used in packaging of various capacities, Such as infusion bottles, vials, and medicine bottles. The tube bottle is a secondary molding process with uniform wall thickness and is lightweight. It is generally suitable for small-capacity packaging. For example, vials, ampoules, prefilled syringes, glass needles, cartridge bottles, oral liquid bottles, etc.
Surface Treatment After Molding
Through neutralization treatment, the concentration of alkali metal ions on the inner surface of the glass is reduced, and the water resistance of the inner surface of the Glass Medicine Bottles container is improved. The water resistance and lubricity of the inner surface of the glass container can be increased after special treatment. Reduce the residue of liquid medicine hanging on the wall. It is beneficial to the piston sliding in the glass needle tube. Through the chemical strengthening process, the mechanical strength of the glass container can be significantly improved and the breakage of the glass container can be reduced. Increase barrier properties and strength with plating or soil layers.
Shape
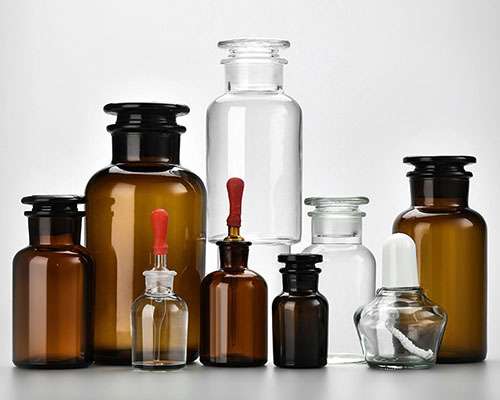
An ampoule is a small glass medicine bottle used to hold medicinal liquids. The Glass Medicine Bottles are made of high-quality thin glass tubes, the top is sealed with an open flame to isolate the air, and the Glass Medicine Bottles’ body is sealed together. It is widely used to hold injectable preparations and high-purity chemicals that must be isolated from the air, such as injectable drugs, vaccines, and serum. It is also used to hold liquid cosmetics.
Glass Vials are commonly used in packaging glass bottles for vaccines. It is sealed with a rubber stopper, a top aluminum cap, and a thin neck. The difference between vials and ampoules is that the bottle mouth is sealed with a rubber stopper, and the overall wall of the bottle is thicker. The vial is named after the medicine penicillin it originally contained and is now generally used for injections, oral liquids, etc. In terms of the manufacturing process, vials are usually molded or controlled.
Cartridges are commonly known as borosilicate glass sleeves for pen syringes. A cartridge bottle is similar to a syringe without a push rod, equivalent to a “bottle without a bottom.” The front of the bottle is equipped with an injection needle protected by a rubber seal, the mouth of the bottle is sealed with a rubber stopper and aluminum cap, and the tail is sealed with a rubber piston. Although the cartridge bottle has no bottom and seems to be an incomplete product in terms of shape, it has met the conditions for sale and use as a complete product.
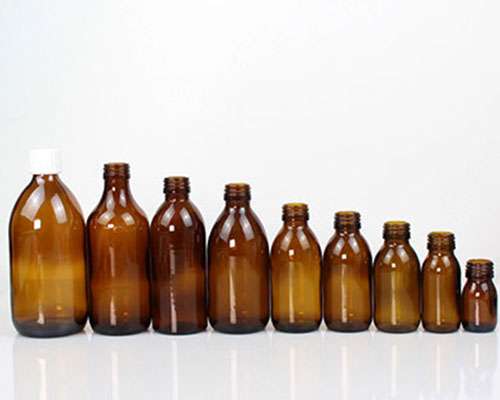
Glass Medicine Bottles Wholesale
Glass medicine bottles are the perfect pharmaceutical packaging material. They are easy to store and come in various very detailed bottle shapes. If you choose glass bottles as packaging material, Taibo Glass Factory is your reliable partner. We insist on producing high-quality glass products and improving service standards. Whether you are an experienced manufacturer or a retailer looking to expand your market, our glass medicine bottles can help. We provide customization services with different requirements such as shape, size, color, etc. Contact us today to explore options for your unique requirements.